If you are planning a DIY deck project, one of the most important parts is building the stairs. Maybe you need to add a short set of steps to reach your back door or a shed. These are projects that you can accomplish yourself, but most of the time, stairs on the inside of the home must be constructed by a licenced contractor. If you are thinking about building a small set of steps for your landscape or outdoor project, this article will help you understand the process.
How easy is it to build steps for a deck?
The answer to how easy is it to build steps for a deck is that it is a manageable process, but some parts of the process require time to get right. Outdoor timber steps are a relatively easy project as far as materials and carpentry skills are concerned. You can always purchase ready-made outdoor steps and attach them to your deck with minimal skills. The most challenging part of how to build steps for a deck is getting the steps level and the proper height. You want to make sure that they are easy to get up and down and do not slant and cause a tripping hazard.
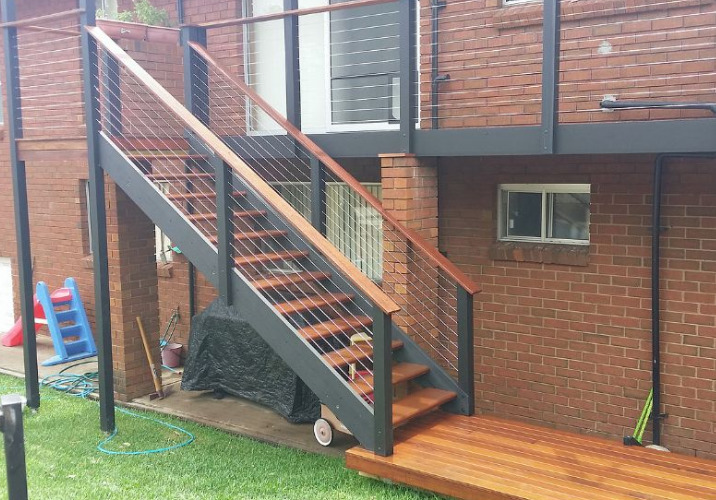
What is the standard rise and run of stairs
Before beginning the process, make sure to check your local building codes, because even for a short set of outdoor deck stairs, some areas have strict regulations. The first thing that you need to know about how to build external timber stairs is the standard stair step height that is required.
The first thing you must do is calculate the proper rise and run for the stairs. This is the most crucial part because it will affect the staircase’s stability and overall usability. The rise is the total height of the stairs from the ground. The run is how far out the stairs will need to go to create stairs that are not too steep and difficult to navigate. The height of each stair is a function of this calculation.
Materials and tools
Here are some of the basic materials and tools you will need to complete your staircase construction. Keep in mind that DIY stairs will require some basic carpentry tools, and purchasing the proper safety equipment is always a must. Make sure that you have all of the required tools and materials on hand before you begin your project.
- Tape measure and carpenter’s pencil
- Carpenter’s square
- Spirit Level
- Cordless drill and decking screws
- Circular saw or hand saw
- Clamps
- Lumber for the stringer, treads, and risers
- Bracket designed to attach the stairs to the deck, house, and flooring
- Paint and approved outdoor sealant
How to build deck stairs
Now that you have your materials, it is time to begin constructing the stairs.
- Calculate the stair rise and run: The first thing you need to do is calculate the stair rise and run. You need to determine how many steps you will need to make the stringers carry the treads and risers. First, measure the total height that the stairs will need to cover. This will be measured from the ground or flooring to the deck’s top board. The standard step height is between 16.5 and 20.3 cm. The best step size for stairs is 17.7 cm on average. Divide the height of the rise by this number. This will tell you how many steps you need. The tread’s width needs to be no less than 22.8 cm so that your entire foot can fit on them. Multiply the number of stairs by the tread width, and this will give you the run of the stairs. This is the length the stairs will extend from the deck or home.
- Measure and cut stringers: Once you have these measurements, it will allow you to cut the stringers accordingly. You will need to accommodate for at least 22.8 cm horizontally, and the stairs’ height. This template will look like a sawtooth pattern. It will have a place for you to attach the treads and risers securely. It is important to make sure that your cuts and measurements are accurate. Otherwise, your stairs could have a slant, which could cause a tripping hazard. This is the most critical part of the building process.
- Install stringers: The first thing that you need to do is to securely attach the stringers to the house or deck and the flooring or ground. If you are attaching to the ground, you will need to get brackets that hold H3 CCA posts. Special brackets will also be needed for attaching to wood or concrete surfaces.
- Install risers: Next, use decking screws to attach the risers to the stringers securely. When installing the risers, make sure that everything is flush and secure. Countersink all of your screws to make sure that none of the heads stick out and can snag on clothing or shoes.
- Install treads: Installing the tread is a step that requires special attention. They should be securely attached with decking screws and countersunk, just as with the risers. Even if you accurately cut the stringers, it is still a good idea to double-check each tread as you install it with a spirit level to make sure that it is flat. Make sure you know how to level stairs before beginning this step.
- Attach trim boards: Now, you can attach the trim boards and give your project a finished, professional look.
- Varnish and seal: The final step is to varnish and seal the decking. Make sure to use a product designed for exterior decking. You should also choose one that will not cause slipping or become slippery when wet. Installing grips to the treads can help prevent a tripping hazard. Now, your deck stairs are ready to use.
Contact local decking experts
How to build interior stairs
Building interior stairs uses a similar process as building outdoor stairs for decks. In some houses, the rooms’ size and way out may make the calculations trickier than for outdoor deck stairs where you have plenty of space. The process is similar, but building codes and stair dimensions are different for the house’s interior than for the outside. Most inside stairs require a licenced contractor for the job.
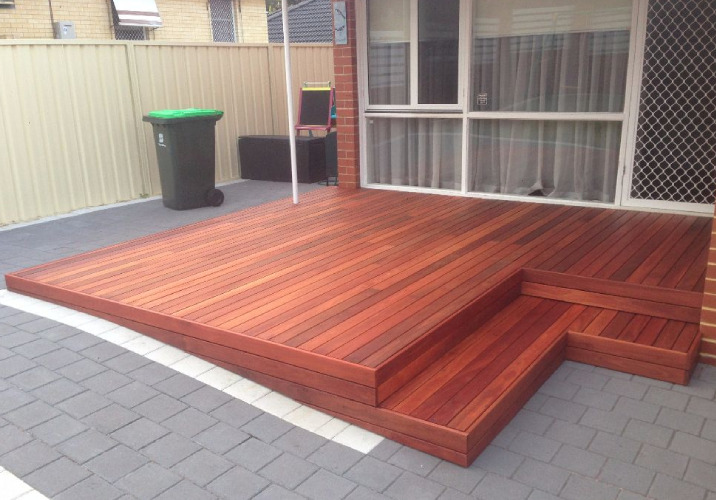
How to hire a builder
As you can see, building a set of stairs looks like an easy process, but it is quite complicated. Suppose you get the calculations wrong or miscut one of the stringers. In that case, you can end up with a set of stairs that is a hazard, look unattractive, and that could land you fine if the inspector happens to see them. Safety is the most important consideration when building a set of stairs, so if you do not have the experience or knowledge to do it right, this is one job that is better left to the professionals.
Licencing and qualifications
Your contractor must have a carpenter’s license and a general contractor’s licence to complete the job. Some locations have special requirements that must be met. It is up to you to make sure that you hire a contractor who is licenced and qualified to complete the job properly so that your stairs will be safe for you and your family.